鋼球加工中燒傷的分析與控制(二)
鋼球燒傷的原因及分析
2 燒傷原因及分析
2.1 機(jī)理分析
鋼球在磨削加工時,其局部表面受到驟然磨削、擠壓、摩擦等強(qiáng)力作用,導(dǎo)致局部溫度瞬間上升過高,而后冷卻形成鋼球燒傷。當(dāng)局部溫度瞬間升高到高溫回火溫度時,又迅速冷卻,產(chǎn)生的燒傷經(jīng)冷酸洗后呈灰黑色,其組織為回火屈式體,這種燒傷被稱為回火燒傷?;鼗馃齻橛芯植繀^(qū)域復(fù)雜的顯微應(yīng)力變化,因而會對鋼球的質(zhì)量(如壽命等)造成影響。當(dāng)局部溫度瞬間升高到淬火溫度時,又迅速冷卻,在該局部產(chǎn)生淬火現(xiàn)象,酸洗后呈灰白色的淬火馬氏體,這種燒傷被稱為淬火燒傷。淬火燒傷會造成鋼球表面局部區(qū)域內(nèi)顯微組織和應(yīng)力的較嚴(yán)重變化,破壞鋼球表面組織和應(yīng)力的均勻性,從而嚴(yán)重影響鋼球的壽命。
2.2 工序分析
鋼球加工中的光球、磨球和研球3個工序都可能產(chǎn)生鋼球燒傷。經(jīng)統(tǒng)計(jì)表明,這3個工序產(chǎn)生燒傷的幾率分別占燒傷總數(shù)的17%,76%和7%。各工序發(fā)生燒傷幾率的統(tǒng)計(jì)數(shù)據(jù)見表1。
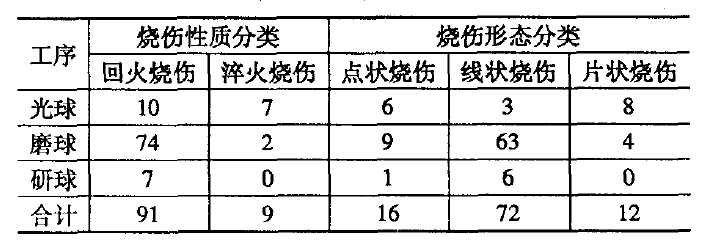
表1 各類燒傷產(chǎn)生的幾率 %
由表1可以看出:
(1) 磨球工序是燒傷發(fā)生幾率最高的工序,也是各鋼球廠控制燒傷的關(guān)鍵工序。其中以線狀回火燒傷為主,點(diǎn)狀燒傷比例也較高,另有少量淬火燒傷。
(2) 光球工序由于壓力大、速度快,產(chǎn)生燒傷比率也較高,特別是光球工序產(chǎn)生的淬火燒傷(如變色球),對鋼球壽命影響最大(但當(dāng)前被不少鋼球廠所忽視)。
(3) 研球工序產(chǎn)生少量的點(diǎn)狀、線狀回火燒傷,由于已接近加工到成品而不好消除,同樣存在影響鋼球壽命的問題。
2.3 鋼球規(guī)格分析
鋼球加工實(shí)踐中,不同規(guī)格鋼球加工產(chǎn)生燒傷的幾率有一定區(qū)別,通過統(tǒng)計(jì)分析表明,鋼球越大,因其自轉(zhuǎn)較差而產(chǎn)生燒傷的比例就越大。對?3.175 ~ 25.4 mm尺寸范圍鋼球產(chǎn)生燒傷(500批次)的統(tǒng)計(jì)結(jié)果為:?3.175 ~ 9525 mm鋼球所產(chǎn)生的燒傷數(shù)約占9%;?10.0 ~ 14.288 mm鋼球產(chǎn)生的燒傷數(shù)約占26%;?15.081 ~ 25.4 mm鋼球燒傷數(shù)約占65%。
2.4 原因分析
點(diǎn)狀、線狀及片狀燒傷產(chǎn)生的主要原因見表2。各類燒傷的直接原因不相同,但其間接原因有時也會混合,引起不同形狀的燒傷。同時,加工過程中人為操作不當(dāng),也是產(chǎn)生各類燒傷的重要原因之一。
燒傷分類 | 直接原因 | 間接原因 |
線狀燒傷 | 鋼球自轉(zhuǎn)不靈活而形成滑動摩擦 | 1. 砂輪板、鑄鐵盤的硬度過高; 2. 鋼球的壓力過小或鑄鐵盤、砂輪溝槽過深; 3. 加工鋼球的溝槽深淺不一致,有的溝道對球的約束力不夠,造成鋼球連動或滑動; 4. 鑄鐵盤入口處喇叭口過于寬大,使鋼球接觸砂輪溝邊沿; 5. 機(jī)床主軸精度、兩磨板的平行度、溝槽的同心度未能滿足要求; 6. 設(shè)備液壓部穩(wěn)定; 7. 鑄鐵盤或砂輪的溝槽不相吻合; 8. 同批鋼球的批直徑變動量大或混入大規(guī)格鋼球; 9. 磨削液潤滑性能過強(qiáng),或混入機(jī)油等導(dǎo)致鋼球連動或滑動。 |
點(diǎn)狀燒傷 | 鋼球受到硬質(zhì)點(diǎn)擠壓、撞擊等 | 1. 鑄鐵盤、砂輪溝道有砂眼、硬質(zhì)點(diǎn)、裂紋或掉粒(塊)等; 2. 鑄鐵盤盤口有尖點(diǎn)或大毛刺; 3. 聚球刀板有尖點(diǎn)或大毛刺,或聚球刀板磨損而聚球不順利; 4. 分配器與鑄鐵盤入口的交接處不吻合,或分配器后退使鋼球在入口處短暫停留、竄溝,而被砂輪的溝沿打傷; 5. 設(shè)備轉(zhuǎn)速太快或速度變化率太大,鋼球突然加速運(yùn)轉(zhuǎn) |
片狀燒傷 | 鋼球受到超強(qiáng)壓力,只公轉(zhuǎn),不自轉(zhuǎn) | 1. 鋼球在分配器和鑄鐵盤入口處進(jìn)球不順暢,在入口處堆積而堵溝,或者因其他原因造成某些溝槽太淺,當(dāng)鋼球重新進(jìn)入該溝槽時產(chǎn)生片狀、兩極燒傷; 2. 換磨加工大規(guī)格鋼球時,未做壓溝處理; 3. 混入大規(guī)格鋼球或機(jī)床上的死角球重新進(jìn)入溝槽。 |