鋼球加工中燒傷的分析與控制(三)
鋼球燒傷的控制
3 燒傷的控制
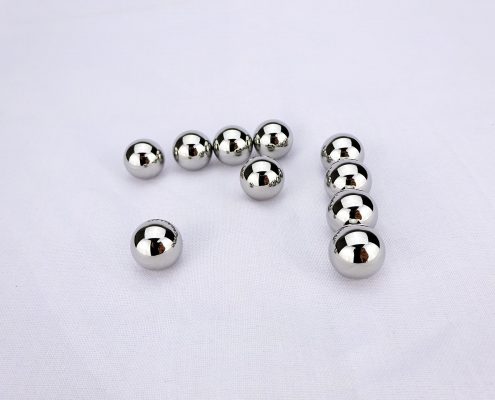
軸承用鋼球
由于鋼球加工中產(chǎn)生燒傷的原因較多,人為因素影響較大,特別是鋼球?qū)倥考庸?,因此,控制燒傷有一定的難度。以磨球加工的燒傷控制為例,提出控制燒傷應(yīng)把握好以下10個(gè)方面,其他工序的燒傷控制可參照。
3.1 熟練的操作工是控制燒傷的前提
控制燒傷要求操作工:(1)責(zé)任心強(qiáng),嚴(yán)格按工藝操作;(2)操作熟練,會(huì)檢查溝槽、盤口、工裝等是否滿足加工要求;(3)能快速分析與解決球出現(xiàn)燒傷的問題。
3.2 高的設(shè)備精度與性能是控制燒傷的基礎(chǔ)
控制燒傷要求加工設(shè)備:(1)主軸精度高,磨床主軸軸向、徑向跳動(dòng)分別要控制在0.05 mm,0.04 mm以內(nèi);(2)鑄鐵盤、砂輪安裝精度高,保證兩板平行度小于0.05 mm,且安裝螺栓都要上緊;(3)液壓系統(tǒng)穩(wěn)定,不出現(xiàn)掉壓現(xiàn)象等;(4)修整器間隙小,修整的砂輪不能有大毛邊、掉塊等,發(fā)現(xiàn)此現(xiàn)象要調(diào)整修整器及金剛石。
3.3 硬磨球進(jìn)出球有序、順暢是控制燒傷的關(guān)鍵
(1)進(jìn)球要平穩(wěn)、順暢,不能堆球而堵溝;(2)進(jìn)球要基本一致,不能有的溝多、有的溝少;(3)出球要順暢,不能有卡球的現(xiàn)象,不能跳動(dòng)太大,能實(shí)現(xiàn)內(nèi)外交換。出現(xiàn)以上問題要立刻停機(jī),按要求檢查并調(diào)整進(jìn)、出球工裝等。
3.4 制作配套的進(jìn)、出球工裝并安裝到位
(1)進(jìn)球工裝要按鋼球規(guī)格制作與使用,不能一套工裝磨幾種不同規(guī)格的鋼球;(2)鑄鐵盤的進(jìn)球盤口一定要與板溝同時(shí)在數(shù)控車床上制作,且分配器安裝與盤口不能錯(cuò)位;(3)進(jìn)球工裝坡度要根據(jù)鋼球規(guī)格選擇,進(jìn)球不能太快,否則,將嚴(yán)重撞擊砂輪;(4)聚球刀板要用尼龍板制作,且無尖點(diǎn)或打毛刺,與砂輪溝緊貼吻合。
3.5 選擇優(yōu)質(zhì)且硬度適中的砂輪及鑄鐵盤
(1)鑄鐵盤的溝道不能有砂眼、硬點(diǎn),更不能有砂輪溝劈壞或毀溝等;(2)選擇適中的砂輪、鑄鐵盤硬度,特別是砂輪的硬度。砂輪的硬度選擇一般要求小球高些、大球低些。
3.6 保證加工鋼球良好的精度儲(chǔ)備
磨球加工中還要注意被加工鋼球的批直徑變動(dòng)量。一方面,控制前工序加工批直徑變動(dòng)量小于0.02 mm;另一方面,采取硬磨1、硬磨2的工藝來實(shí)現(xiàn)上下兩批加工球更好的溝槽吻合度。
3.7 選擇磨板的最佳溝槽深度
加工硬磨球的溝槽深度應(yīng)為 (1/3 ~ 2/5) Dw。太深會(huì)出現(xiàn)嚴(yán)重的一圈圈的現(xiàn)狀燒傷;太淺則易出現(xiàn)片狀、兩極燒傷。若溝深,可通過車板或修砂輪加以解決;若溝淺,可以用球壓溝加以解決;深淺不一可采用壓溝解決。
3.8 選擇合適的主軸速度
由于現(xiàn)行的磨球機(jī)大多是固定幾個(gè)檔位的速度,加工中變速會(huì)使鋼球與溝槽的相對(duì)速度突然變化,從而產(chǎn)生燒傷。解決辦法為:(1)硬磨加工完工前,高中低速變檔時(shí)間要早,至少留0.02 mm,或一直用中速加工到完工尺寸;(2)采用兩段硬磨工藝,第二段硬磨時(shí)采用中速、不變速;(3)選擇主軸是無級(jí)變速的磨球機(jī)。
3.9 選擇合適的壓力
加工硬磨球,應(yīng)根據(jù)溝槽深度、被加工球的規(guī)格,選擇壓力范圍(2 ~ 3 MPa),壓力不好掌握的,以電流20 ~ 25 A為宜。同時(shí),硬磨球加工中壓力要穩(wěn)定,不能升降壓,否則易出現(xiàn)燒傷。
3.10 嚴(yán)格控制硬磨液
(1)硬磨液配比要符合工藝,以鋼球加工效率進(jìn)行控制,加工效率以0.015 mm/h左右為宜;(2)要做好硬磨液的過濾,特別不能有機(jī)油混入;(3)要選擇硬磨液溫度正常時(shí)加工硬磨球,一般以25 ~ 40 攝氏度為宜,不能過冷或過熱。
4 結(jié)束語
鋼球燒傷可直接導(dǎo)致鋼球及軸承壽命的降低。鋼球燒傷的控制重在預(yù)防,只要按照燒傷控制的10個(gè)方面做好預(yù)防,真正做到工藝規(guī)范化、裝備標(biāo)準(zhǔn)化、操作一致化、原輔料質(zhì)量穩(wěn)定,就能有效控制好鋼球燒傷。